Stucco can keep your home warm in the winter and cool in the summer. However, Stucco Charleston SC must be properly installed. Code requires a weather-resistant barrier to be applied over wall sheathing. There are several code-recognized materials to use for this purpose. It is also critical that the surface be wetted before plastering.
Scratch Coat
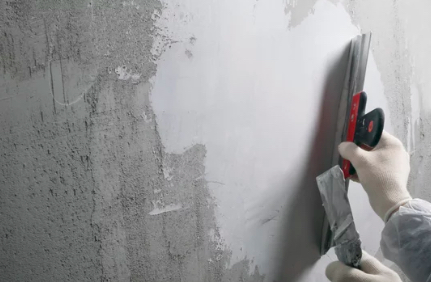
Whether stucco is applied to wood sheathing, masonry, or brick, a first layer known as the scratch coat must be hung to provide something for the subsequent coatings to adhere to. Without it, the next layers- the brown coat and finish coat- may not bond well, leaving the veneer loose or prone to water infiltration.
The scratch coat is hung using a square trowel, aiming to make it roughly 5 millimeters thick. After hanging, it must be scraped horizontally and vertically to create a rough surface that the brown coat can “key” into. A good mix of sand and cement helps to form this base layer. It can also contain one of many color-enhancing dyes to create a unique appearance, although this is not necessary with most stone veneer installations.
Once the scratch coat is stiff, it is sprayed with a fine mist of water to keep it moist for the duration of its cure. A moisture level of about 48 hours is ideal, and the plaster should never be allowed to dry out completely or it will be susceptible to failures that could affect long-term strength.
Some contractors use the double-back method of installation, applying the brown coat as soon as the scratch coat is stiff, but this is not recommended if the weather is cold or rainy, as these conditions slow the strength-building process. The second coat is known as the brown coat, and it is made of a mixture that is similar to the scratch coat but thicker.
Brown Coat
A brown coat is a thick layer of cement-like stucco that looks more like concrete than plaster. It is a necessary part of the stucco process and provides a solid foundation for your finish. The brown coat is made of a mix that includes Portland cement, sand and fibers. This mix is a faster alternative to three-coat stucco and saves you time and money.
The brown coat must be cured for a period of time after it is applied. This process is called moist curing and involves spraying the walls with a fine mist of water to keep it from drying out too quickly. This step is particularly important in hot weather when the stucco may dry out and become susceptible to damage from sunlight or wind.
After the scratch coat has been cured, it is ready for the brown coat. The brown coat is applied in a grid pattern across the wall. This allows the plasterer to control the thickness of the coating and helps achieve a uniform look. A tool called a darby is used to apply the brown coat. It is a three foot long trowel with two handles mounted on it that is used to push the cement down and out to prepare it for the next phase of the stucco process.
A good brown coat is essential for a great finished product. It is important that the brown coat be flat with minimal voids and variations. This is especially important with fine grit synthetic finishes where the brown coat needs to be rodded in order to ensure that the float process will fill any voids.
Finish Coat
The finish coat is the last step of a traditional three-coat stucco application. It is applied with a brush or roller and gives the project its final esthetic appearance. Careful preparation with fine sandpaper (220 grit or higher) and sanitation in the work area can save time by eliminating the need to scrape off excess material before applying the last “look” coat.
Traditionally this last coat has been made from various types of plaster and requires the addition of sand and lime. The resulting mixture can be troweled, smoothed, scraped or floated in a variety of textures to produce the desired result.
A newer method called one coat stucco is gaining popularity because it speeds up the original process by combining the scratch and brown coat into a single application of 3/8’’ to 1/2’’ thick. One coat stucco still provides all the same benefits as three-coat, such as design flexibility, durability and fire resistance.
A high-quality, preblended, Portland cement-based finish mix is typically used as the finishing coat for two and three-coat stucco applications. It is pigmented during the blending process to create a uniform look. The finish is a water-resistant product that will require no additional coatings for performance or color retention. It will also resist damage caused by surface abrasion, wind and rain. However, it will require a proper base and build coat for long-lasting performance.
Wire
Lath is a metal or fiberglass mesh that provides the base for which stucco can be applied. It comes in a variety of sizes and materials, and is usually galvanized to prevent corrosion. It may be woven together in a pattern similar to chain link fencing, or twisted and welded in place. Stucco contractors use it for the outer walls of homes and buildings, but they also use it to construct fences, trellis and awnings. It’s popular among set designers and sculpture artists because it holds its shape well and is relatively light.
Most traditional stucco contractors prefer to use galvanized 4 penny nails or staples for fastening lath to wood and masonry surfaces. The nails are driven in halfway or more and then bent over, a process known as “tonguing.” This helps to prevent the nail from becoming loose and falling out. In addition, it helps to create a space between the sheathing and the wall to allow water to escape when it is needed.
Stucco can be difficult to install without the help of a professional. A reputable stucco contractor will be able to do the job quickly and efficiently, saving homeowners money in the long run. They can also provide warranties for their work, giving homeowners peace of mind that if problems occur, they’ll be able to fix them. Additionally, a professional can give advice on the best type of stucco for the climate in which you live.